Castings SA – January
More efficient furnaces drive significant energy, cost and time savings at PDC
Posted on 14 January 2020 by castingssa
“Like every business and manufacturing operation in South Africa we were experiencing frustrating times when confronted with Eskom’s power outages and planned load shedding that have been haunting us for several years now. But it is not just the inconvenience of trying to work in the dark that raises temperatures (excuse the pun) it is also the repercussions of the resultant failures of machinery and equipment,” explains Mike Wolhuter of Pressure Die Castings (PDC).
“South Africa and its people have been induced into a sleepwalking mode by our not so efficient SOE and we are all counting the consequential cost. You can remain in your slumber or you can be proactive and investigate and implement solutions. We have chosen the latter as molten metal at the right temperature is critical to our business, as it is to all foundries. Surprisingly, you will be astounded at the other savings and process improvements that you will achieve once you have decided on your solution to reduce management and staff stress levels. So at least we can thank Eskom for forcing us into this situation,” adds Wolhuter.
Brass holding furnace improvements
“PDC is an innovative supplier of brass, aluminium and zinc castings to the South African and international markets that has been in business since 1952. We are a specialised high-pressure die-caster that explores the needs of a customer to identify and offer the best design and process solution. This can be for as cast or final machined component or for the final assembled product and this includes all the associated processes.”
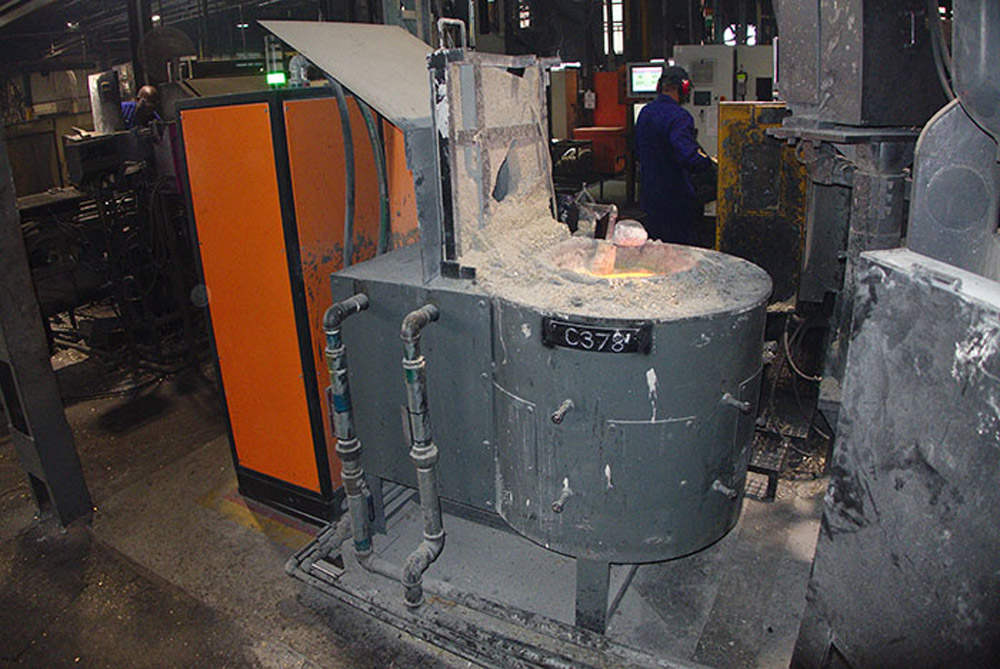
Pressure Die Castings is introducing coreless induction holding furnaces into its brass foundry
“Primarily we are a high-pressure die-caster of brass components. We process approximately 100 tons per month of brass and have extensive experience in the manufacture of alloys that contain about 60% copper, including De Zincification Resistant (DZR) brass. DZR has alloy additions that resist the leaching of zinc out of the brass where water is present. Component sizes range from a few grams to just under 1kg with production volumes exceeding well over a million components per month.”
“These are big numbers and any breakdown in our processes can be consequential. Our 14 high-pressure die-casting machines are hungry beasts and need to be fed regularly. Although understanding, clients do not want you to make your problems their problems. Problems such as the breakdown of some of our channel holding furnaces. These problems occurred because of Eskom’s load shedding programme.”
“So we tasked Fred Cooper and Deon van Staden to come up with a solution.”
Fred explains: “The HPDC foundry industry relies on the holding furnace to hold a certain volume of metal at the correct temperature, so that the correct dose of metal can be delivered to the casting machine at the correct temperature for the product being cast. The volume contained in the holding furnace is a buffer volume to allow the casting machine to operate continuously, whilst a fresh batch of primary melt is being prepared to top up the holding furnaces at a later time.”
Existing channel induction holding furnaces
“For the brass HPDC foundry at PDC, the holding volume is typically 800kg of brass, and the temperature required to cast product is in the region of 970C. The furnace is a channel induction type of furnace, with a box type of tundish to hold the working volume of molten brass. A channel of molten brass loops from the bottom of the tundish around an induction coil and laminate core system, much like a transformer. The channel forms a one turn to the secondary side of the transformer and the coil within forms a multiple turn to the primary side of the transformer.”
“The channel receives energy induced by the primary coil, and the localised heat and induced current in the channel sets up convection currents that circulate out into the tundish, drawing in cooler metal from the tundish at the same time. The circulation is continuous whilst power is applied to the primary coil.”
“The furnaces were built from technology as old as the transformer itself, from an age where the power control used was physically changing tapped voltages from an adjacent transformer. The casting operators changed the tap settings themselves to regulate the metal temperatures delivered to the casting machines.”
“Advances in power electronics have allowed advancements in furnace temperature control. Efficient power control has allowed for accurate metal temperature control, without operator intervention.”
Limitations with channel furnace
“The recent load shedding programmes from the national electricity supplier had led to failures of these furnaces. Channel furnaces are best left to remain molten at all times, 24/7. Should a furnace be allowed to solidify, the channel loop tends to crack due to shrinkage when the phase changes from liquid to solid. The cracked channel breaks electrical continuity and the transformer principle no longer functions. Therefore, no energy can be induced into the melt.”
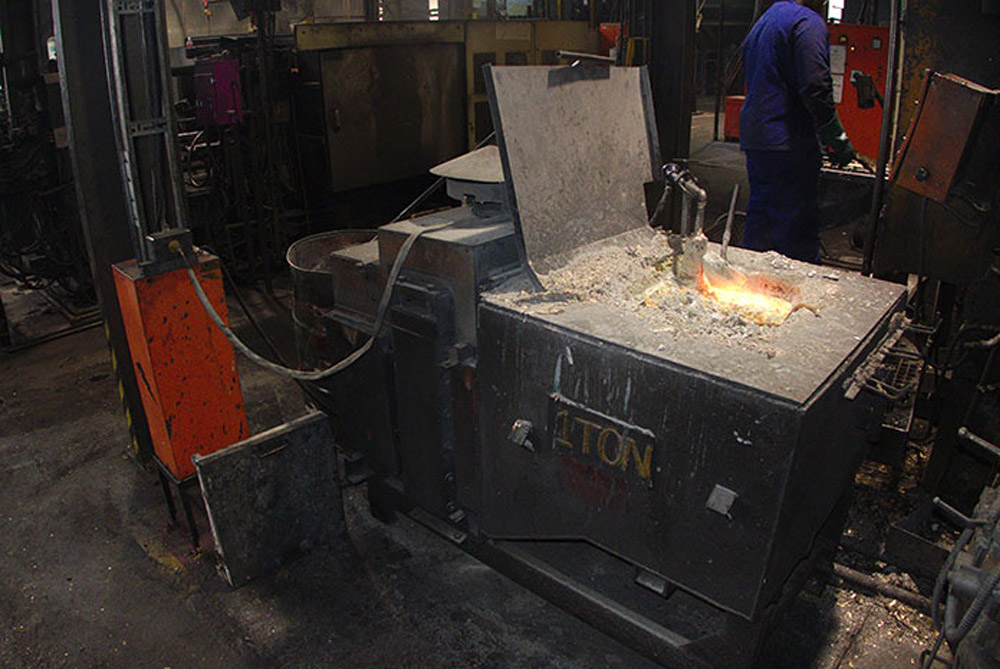
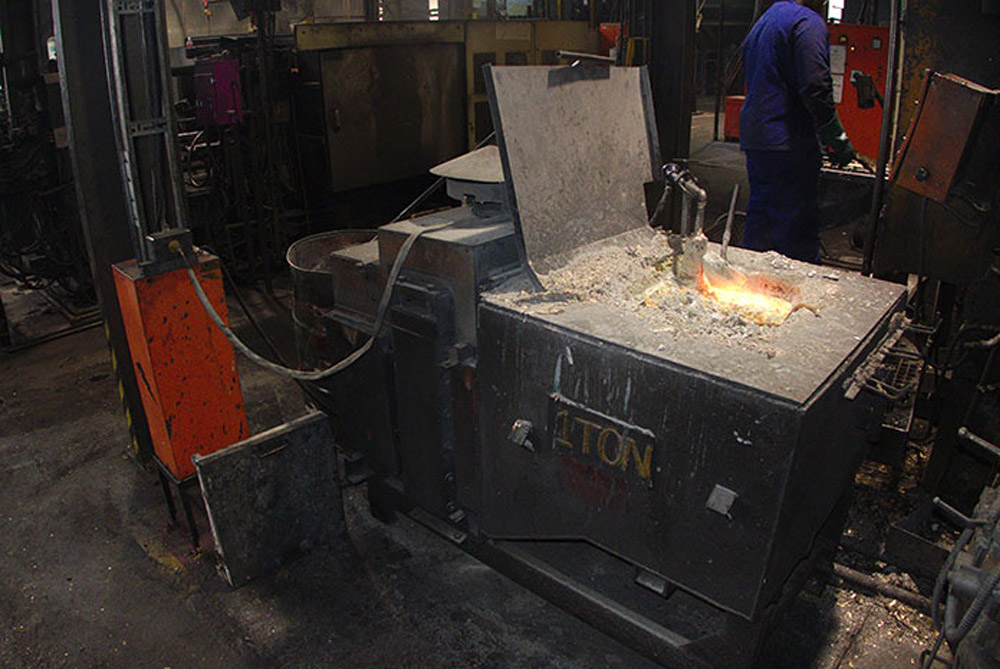
The existing channel furnaces at Pressure Die Castings have many limitations that were identified during an 18 month investigation
“Those furnaces that do survive a power outage and maintained electrical continuity, require long periods of reheating back to operating temperature. If the temperature ramp up is too rapid, whilst the channel/tundish is in a solid phase, localised heating causes localised softening of the channel. Sometimes the channel cracks and breaks the electrical continuity.”
“Repairing a furnace requires a complete breakdown to the shell of the body, and reconstruction from scratch. A brass former of the channel needs to be cast and the tundish needs to be rammed with new refractory around the cast channel. After ramming by technicians experienced in the practice, the furnace needs to be dried and sintered for days before it can be placed into service. The first melt also requires days of heat up to prevent hotspots developing in the channel.”
“Additionally, the heating rate of the channel furnace from solid had to be restricted to prevent failure of the channel. After the event of a power outage or shutdown, it would take a couple of days to have the furnace ready for production. The loss of production due to reheating was therefore quite significant.”
“The costs of electricity powering these furnaces demanded an in-depth study into the running costs and efficiencies of the channel induction furnaces in the foundry. The result determined that the channel furnaces were at best 18% efficient and required an estimated R65 000 per month in electricity costs for a full production month.”
“The channel furnaces are connected in a 2-phase supply configuration. This created an imbalance of the 3-phase supply of the factory reticulation, and careful planning of the electrical layout was required. The net result was an increased peak demand requirement to cater for the imbalance in phases.”
Replacement furnaces – Coreless induction holding furnaces
“A different approach to holding metal was investigated to minimise the losses and limitations of the current practice. It was reasoned that the best option for the PDC foundry was the coreless induction type furnace, sized to the needs of the HPDC process.”
“The coreless induction furnace is essentially a cylindrical tundish, with a large induction coil circling the tundish. The coil is powered by high frequency drivers inducing current into the melt, which in turns heats up and stirs the melt. The molten metal remains one unified volume, unlike the channel furnace, which has a looped branch for the channel.”
Improvements with the coreless furnaces
“The body construction of the coreless furnace was simpler and smaller and allowed a reduction of holding volume to 400kg of brass. It was later determined that this was below the requirements of the PDC foundry and a body of 600kg brass was substituted. Despite the adjustment, the holding volume is less than that of the channel holding furnace. The temperature required to cast product remained in the region of 970C.”
“When the furnace is powered down, the melt simply solidifies and contracts into the unified volume without damaging the furnace. The furnace then may simply be powered up with an appropriate ramp up cycle, to prevent dangerous bridging, a topic for another discussion. It has been demonstrated that this ramp up time takes a matter of hours. After a power outage or planned shutdown the melt is ready for production in a matter of hours. This is a significant gain over the channel furnace.”
“Should damage to the furnace occur, such as an electrical short due to over filling, or a cooling water leak, the recovery of the slug and breakdown of the lining is a simpler procedure. Relining of the body commences without a complete breakdown required. The relining of the body is a quicker process, as are the heat up and sintering stages when compared to the channel furnace.”
“A study into the running costs determined that the coreless induction holding furnace was 36% efficient at best, and required an estimated R52 500 per month in electricity for a full production month.”
“Other advantages include a higher melting rate – 300kg per hour as compared to 80kg per hour – and the channel furnace could be out of service between five and seven days as compared to us having the coreless furnace up and running within 12 hours.”
“The frequency driver for the coreless induction furnace is now connected in a 3-phase configuration. This has allowed for a more balanced electrical reticulation in the factory, and a reduction in peak demand requirements.”
“Additionally, the coreless design does allow for the furnace to be bailed down and powered down over periods of shutdown and periods of no production. This further reduces running costs without the risk of damaging the furnace and an expensive rebuild, as experienced with the channel furnaces.”
“Two furnaces have already been converted to coreless and we will shortly begin converting a third furnace. The decision has been set to convert all furnaces to coreless, in time.”
“We took roughly 18 months to investigate options, agree on R&D terms, build and commission at PDC, troubleshoot and redesign power and controls. The resultant solutions have now enabled management and staff to smile again. They are no longer as highly strung as a high-pressure die-casting machine,” concluded Cooper.
For the original article please visit www.castingssa.com